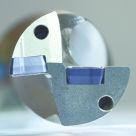
WNT UK’s latest high performance indexable insert drilling system, the C900 high feed drill with its use of a single style, grade and geometry for the central and peripheral insert is a combination that is not just increasing productivity, but reducing inventory and manufacturing costs as well.
The indexable insert drill is providing users with a universal, stable, economical platform to produce holes cost-effectively. By making use of just one insert design, one grade of carbide and one geometry, WNT is helping to drive down manufacturing costs without impacting on productivity. Each insert has up to four cutting edges and is manufactured from CCN 1430 grade carbide with a PVD coating, which provides the optimum combination of toughness and wear resistance required for the drilling process.
By limiting the C900 high feed drill to a single insert style WNT claims it is reducing inventory costs and eliminating potential operator error, while at the same time creating a drill capable of producing holes at up to 5x diameter. The design of the drill body also plays an important role in process stability and the flutes of the C900 are designed to work in conjunction with the insert geometry to give maximum chip flow. Cutter life is also extended through the use of WNT’s Highlight coating, which protects the drill body from abrasion.
Available as standard in either 3, 4 or 5x diameter drill depth configurations with diameters ranging from 19mm through to 36mm in 1mm increments, the C900 high feed drills can be used to drill holes in uneven, inclined and convex surfaces and can handle cross holes, welded seams and chain drilling operations.
“The C900 is typical of the tooling developments that WNT introduces as we are always looking at ways of simplifying processes for our customers, improving productivity and reducing costs,” says Tony Pennington, managing director of WNT UK. “With the C900 we achieve all of this in a single tool.” |